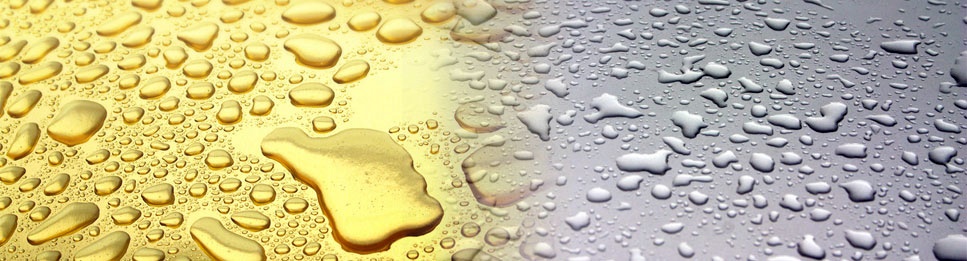
Как подготовить поверхность к покраске? Какие инструменты, материалы и составы использовать? Общие вопросы техники безопасности.
Перед окраской любыми методами поверхность должна быть очищена от жировых загрязнений, средств консервации, смазочно-охлаждающих жидкостей, а также от окалины, ржавчины и неорганических солей; желательно наличие на поверхности слоев (фосфатных, хроматных и др.), улучшающих адгезию лакокрасочного покрытия и удлиняющих срок его службы. Чем агрессивнее среда, в которой эксплуатируются покрытия, тем тщательнее должна быть подготовлена поверхность.
Минимальная толщина лакокрасочного покрытия должна на 20% превышать максимальную высоту микронеровностей. При излишней шероховатости повышается расход лакокрасочного материала, но срок службы покрытия при этом не увеличивается. Чаще всего коррозия начинается на пиках поверхности, слабо укрытых лакокрасочным материалом. Величина показателя доступности зависит от метода обработки поверхности.
Материал и способ обработки | Шероховатость поверхности — показатель доступности | Шероховатость поверхности — Ra | Шероховатость поверхности — Rz |
Жесть черная полированная на аноде | 3,9 | 0,02—0,16 | 0,1—0,2 |
Жесть черная полированная | 5,6 | 0,04—0,63 | 0,2—0,32 |
Жесть черная травленая | 12,1 | 0,2—3,0 | 1 — 12 |
Жесть черная дополнительно фосфатированная | 14,8 | 7,15 — 18,5 | 30—75 |
Жесть черная обработанная щеткой | 35,2 | 0,4—3,5 | 2—14 |
Сталь, обработанная наждачной бумагой | — | 0,06—5,0 | 0,3—20 |
Сталь, обработанная иглофрезами | — | 2,5—7,5 | 10—30 |
Сталь, обработанная песком | 90,4 | 0,4 —8,0 | 2—32 |
Сталь, обработанная галтовкой | — | 0,8 —4,0 | 4 — 16 |
Rz — высота неровностей — среднее расстояние между находящимися в пределах базовой длины пятью высшими точками выступов и пятью низшими точками впадин, измеренное от линии, параллельной средней линии профилограммы (ГОСТ 2789—73 «Шероховатость поверхности»).
Максимальная величина шероховатости поверхности, приемлемая для окраски, равна 40 мкм. Величины Ra и Rz зависят от таких технологических факторов, как состав полировочных паст и режимы полирования, состав травильных растворов и режимы травления, тип щеток н технология обработки щетками, гранулометрический состав, твердость и скорость подачи абразива при абразивной обработке и т. д.
Наиболее широко распространены физико-химические (чаще их называют просто химическими) и механические методы подготовки поверхности. Реже применяют термические методы.
Метод подготовки выбирают в зависимости от многих факторов и на основании технико-экономических расчетов. Стоимость обработки не всегда является определяющим фактором, так как экономия, достигнутая путем снижения качества обработки, может дать убытки из-за снижения срока службы покрытия.
При недостатке производственных площадей можно совмещать химические операции, например травление с обезжириванием, обезжиривание с фосфатированием (для изделий со слабо зажиренной поверхностью), обезжиривание с пассивацией. От выбора способа подготовки также будет зависеть цена покраски порошковой краской.
Материал | Дробепескоструйная очистка (металлическим песком) | Обезжиривание | Дробеметная | Очистка механизированным инструментом | Галтовка | Газопламенная очистка | Травление | Фосфатирование |
Стальной прокат | + | + | + | + | + | + | + | + |
Стальное и чугунное литье | + | + | + | + | + | + | — | — |
Сталь оцинкованная | — | + | — | — | — | — | — | + |
Сталь кадмированная | — | + | — | — | — | — | — | + |
Алюминий и его сплавы | + | + | — | + | — | — | + | + |
Медь и ее сплавы | + | + | — | + | — | — | + | — |
Пользуясь данной таблицей, необходимо иметь в виду следующее:
- Дробеструйный и дробеметный методы очистки допускается применять для узлов и деталей с толщиной стенки не менее 3 мм, газопламенный — при толщине стенки не менее 6 мм.
- Для изделий сложной и особо сложной конфигурации не рекомендуется применять стационарные дробеметные установки.
- При выборе химических методов подготовки поверхности необходимо учитывать возможность организации процесса нейтрализации отработанных травильных растворов и стоков.
- В условиях серийного и единичного производств допускается применять растворы фосфорной кислоты для травления стального проката со сварными соединениями.
- При фосфатировании изделий со сварными соединениями необходимо проверять прочностные характеристики сварных швов.
- После травления литья требуется тщательно отмывать поверхности от солей и кислот.
- Для обезжиривания алюминия не допускается применять сильно щелочные растворы и трихлорэтилен.
- Для подготовки алюминия под окраску более эффективно хроматирование, чем фосфатирование.
- Абразивная обработка алюминия производится дроблеными фруктовыми косточками или стеклянными шариками.
- Сварные швы при всех методах обработки должны быть дополнительно зачищены и защищены фосфатирующими и другими грунтовками.
Влияние метода обработки поверхности на долговечность лакокрасочного покрытия по стали
(толщина слоя покрытии ~100 мкм)
Метод обработки | Срок эксплуатации покрытия, годы |
Без обработки | 0,5-1,5 (без наличия ржавчины) |
Щетками (вручную) | 1-1,5 |
Механизированным инструментом | 2-2,5 |
Травление | 6-8 |
Пескоструйная | 10-11 |
Обезжиривание
Под термином «обезжиривание» обычно подразумевают удаление с поверхности изделий не только жировых веществ, содержащихся в полировочных составах, эмульсионных охлаждающих жидкостях, консервационных и штамповочных смазках, но и следов пота, солей, остающихся на поверхности после промывок, шлама после травления и др.
При подготовке поверхности под окраску различают три степени зажиренности изделий.
- Слабая — легкие неравномерные загрязнения маслами и пылью при межоперационном хранении;
- Средняя — небольшой равномерный слой смазки, охлаждающих эмульсий с металлической стружкой; образуется при механической обработке;
- Сильная — слой нагаров масла после термообработки, толстые слои консервационной смазки, трудноудаляемые графитовые смазки и т. п.
Выбор метода обезжиривания определяется видом загрязнений, требуемой степенью очистки, воздействием моющего состава на обрабатываемый металл, безопасностью при работе и стоимостью.
Наибольшее распространение получили методы обезжиривания органическими растворителями, щелочными растворами и эмульсионными составами.
Обезжиривание органическими растворителями. В индивидуальном, а иногда и в серийном производствах поверхности обезжиривают, протирая ветошью, смоченной бензином или уайт-спиритом, хорошо растворяющими минеральные масла и консервационные смазки. В этом случае удовлетворительное качество обеспечивается лишь при условии тщательного контроля чистоты растворителя, так как растворяющая способность его резко снижается при содержании в 1 л более 5 г минерального масла.
Применение указанных растворителей связано с взрыво- и пожароопасностью. Огнеопасные растворители иногда заменяют негорючими растворителями — хлорированными углеводородами со сравнительно низкой температурой кипения. С помощью этих растворителей можно обрабатывать изделия как в жидкой, так и в паровой фазах. В промышленности применяют трихлорэтилен (ТХЭ), перхлорэтилен (ПХЭ) и хлористый метилен (метиленхлорид), наиболее часто — трихлорэтилен.
Технологический процесс состоит из следующих операций: обработки в жидком растворителе (с температурой от комнатной до кипения) методом окунания или распыления; обработки в паровой фазе. Последнюю обычно используют в качестве заключительной, когда пары растворителя, свободного от загрязнений, конденсируются на поверхности изделия и обеспечивают высокое качество очистки.
Чаще других применяют процессы по схеме «нагретый жидкий растворитель — пар», распространена также схема «нагретый жидкий растворитель — струя холодного растворителя — пар» для очистки изделий сложной конфигурации.
Изделия из алюминия и его сплавов обрабатывают не ТХЭ, а ПХЭ, поскольку алюминий образует с ТХЭ взрывоопасные смеси.
В зависимости от степени зажиренности изделий применяют различные способы обработки хлорированными углеводородами.
Обезжиривание в хлорированных углеводородах применимо как для мелких деталей, обрабатываемых в корзинах, так и для крупных деталей, обезжириваемых в проходных камерах.
Важной особенностью этих растворителей является возможность регенерировать методом простой перегонки, после чего следует проверить pH водной вытяжки, который должен быть около 7 единиц. При снижении этой величины необходимо произвести дополнительную стабилизацию растворителя триэтиламином.
Стабилизированные хлорированные углеводороды не оказывают коррозионного воздействия на. сталь и цветные металлы.
Все хлорированные углеводороды токсичны. При работе с ними необходимо руководствоваться правилами техники безопасности и производственной санитарии при производстве металлопокрытий. В помещениях не допускается работа с открытым пламенем, так как возможно образование фосгена. Допустимая концентрация паров ТХЭ и ПХЭ в воздухе 10 мг/м3.
Щелочное обезжиривание. При введении в водные щелочные растворы поверхностно-активных веществ (ПАВ) резко повышается их моющее действие вследствие способности ПАВ адсорбироваться на металлической поверхности и менять скорость обмена веществ между металлом и моющим раствором.
Состав моющего раствора определяется видом загрязнения, металлом, требуемым качеством очистки, условиями ведения процесса.
Моющие композиции (моющие средства) состоят в основном из смеси неорганических солей и набора ПАВ; обе составные части влияют на ихнологические свойства растворов.
Содержание ПАВ в щелочных растворах на более 10%. Чаще других применяют смеси анионоактивных и неионогенных ПАВ.
В случае обезжиривания распылением поверхности перед фосфатированием должны быть обеспечены условия для формирования равномерной плотной мелкокристаллической фосфатной пленки. Поверхность не должна пассивироваться при обезжиривании, поэтому pH моющего раствора должен быть не более 11.
В растворы для обезжиривания распылением перед фосфатированием не рекомендуется вводить силикаты, отрицательно влияющие на качество фосфатного слоя.
Увеличение времени обработки свыше 5 мин при обработке распылением и свыше 20 мин при обработке в ваннах нецелесообразно; в таких случаях необходимо изменить состав раствора.
При заметном ухудшении качества обезжиривания (при прочих равных условиях) отработанный щелочной раствор сливают. Частота слива зависит от многих факторов и определяется для каждого технологического процесса.
Средний расход моющих композиций должен находиться в пределах от 2 до 5 г/м2 обрабатываемой поверхности. Регенерировать щелочные растворы экономически нецелесообразно.
Зависимость качества очистки от ряда факторов.
Фактор | Характер воздействия |
Температура моющего раствора | При повышении температуры до 70° С ускоряется процесс очистки; дальнейшее повышение нецелесообразно |
pH моющего раствора | Влияет на моющее действие, выбирают в зависимости от состава раствора и очищаемого металла |
Способ подачи моющего раствора | Распыление, перемешивание раствора, перемещение деталей ускоряют процесс очистки |
Жесткость воды | Ухудшает качество очистки |
Чувствительность металла к коррозионному воздействию моющего раствора | Требует специального выбора pH и состава моющего раствора |
При повышенной жесткости воды качество обезжиривания ухудшается вследствие осаждения на поверхности изделия трудноудаляемых солей кальция и магния. Наиболее доступным способом смягчения воды является введение триполифосфата натрия.
Качество обезжиривания в производственных условиях определяют визуально по смачиваемости поверхности распыленной струей или протиркой белой салфеткой. В лабораторных условиях можно применять другие методы — весовой, фуксиновый, люминесцентный, с помощью радиоактивных индикаторов и др.
После обезжиривания щелочными растворами поверхность промывают водой; от качества промывки во многом зависит долговечность лакокрасочного покрытия. Остатки солей на окрашиваемой поверхности способствуют проникновению влаги сквозь покрытие, развитию подпленочной коррозии. На поверхности изделия остается моющий раствор, количество его зависит от конфигурации изделия и должно быть учтено при технологических расчетах и установлении скорости протекания воды в промывочных зонах агрегатов.
Количество переносимого с изделием раствора можно уменьшить, если рационально подвесить изделие или просверлить отверстия для стока раствора. Промывка должна быть организована так, чтобы суммарное содержание солей в промывной воде не превышало 100 мг/л.
При каскадных промывках снижается расход воды (каскадной или многоступенчатой называется промывка, при которой вода из третьей промывочной ванны подается во вторую, а из второй — в первую). Чистую воду следует подавать из расчета 25—50 л на 1 м2 обрабатываемой поверхности. Повышение температуры воды выше 60° С нерационально, так как растворяющая способность при этом не повышается, а из воды могут выделяться труднорастворимые соли и оседать на отмываемой поверхности. После щелочного обезжиривания можно применять холодные промывки, например две последовательные. Перенос моющего раствора в зону промывки сокращается при проточной промывке струей холодной воды в течение 5—10 с; при этом с поверхности удаляется около 80% щелочного раствора. Следующей в этом случае является промывка с рециркуляцией воды.
Эмульсионное обезжиривание — комбинированный способ, сочетающий достоинства органических растворителей и водных щелочных растворов. Эмульсионные составы представляют собой эмульсии растворителей в воде, стабилизованные поверхностно-активными веществами. Чаще других используют эмульсии хлорированных углеводородов: ПАВ, которые применяются в щелочных составах. В промышленности эмульсионные составы используют для снятия трудноудаляемых загрязнений, консистентных смазок, нагаров масел, старых лакокрасочных покрытий. Эмульсионные составы на основе хлорированных углеводородов не горючи, не взрывоопасны.
При наличии ПАВ в эмульсионном составе загрязнения быстрее удаляются без повторного их осаждения на изделии. Процесс очистки может производиться как при нагреве до 50° С, так и при комнатной температуре.
Применяя метиленхлорид и ТХЭ в эмульсиях, можно удалять многие виды лакокрасочных покрытий, такие как пентафталевые, меламиноалкидные и др. В эмульсионных составах лакокрасочное покрытие частично растворяется и нарушается его связь с поверхностью, в результате чего покрытие отслаивается через 15—20 мин после погружения изделия в ванну с эмульсией. Во многих случаях такой процесс может заменить удаление старых лакокрасочных покрытий в концентрированных растворах едкого натра при высоких температурах.
Эмульсионные составы, загущенные карбоксилметилцеллюлозой (КМЦ), можно применять для удаления лакокрасочных покрытий с вертикальных поверхностей.
Контроль и корректировка растворов в ваннах обезжиривания. Аналитический контроль щелочных обезжиривающих растворов производится 1-2 раза в день. Щелочность раствора определяют путем прямого титрования его 0,1 н раствором соляной кислоты в присутствии индикаторов — бромкрезолового зеленого или метилоранжа. Количество соляной кислоты в миллилитрах, израсходованное на титрование 10 мл щелочного раствора, характеризует его щелочность, в условных единицах (точках). Нецелесообразно аналитически определять отдельные составляющие щелочного раствора. Щелочные растворы корректируют исходным моющим средством при снижении щелочности на 1—2 точки. Смену щелочных растворов производят по мере их загрязнения и снижения моющего действия. Частоту смены устанавливают опытным путем (обычно 1 раз в 1—2 недели).
Травление черных металлов
Процесс травления может производиться путем окунания изделий в ванны или распылением травильных растворов в установках туннельного типа. Для травления изделий, не имеющих сварных швов, следует применять соляную, серную, а лучше ортофосфорную кислоту.
Одним из недостатков травления растворами кислот является необходимость нейтрализации и специальной обработки большого объема сточных вод. Поэтому на многих машиностроительных заводах применение травления ограничено.
Скорость процесса травления зависит .от толщины и состава окисных слоев на металлической поверхности.
Наличие дефектов в окалине приводит к неравномерности травления, которая устраняется введением ингибиторов в травильные растворы.
При травлении распылением по сравнению с травлением в ваннах можно в 2—3 раза повысить производительность, снизить (до 2%-ной) концентрацию травильных растворов, повысить их температуру, работать при повышенных концентрациях солей железа в травильном растворе без снижения скорости очистки. Так, скорость струйного травления заметно не изменяется при содержании железа 200—300 г/л в растворах соляной и серной кислот; для растворов ортофосфорной кислоты эта величина составляет 15—25 г/л. В обычных травильных ваннах скорость травления уменьшается при содержании железа
Вследствие ограниченной растворимости солей железа в фосфорнокислых травильных растворах необходимо непрерывно их регенерировать ионообменными смолами. Этот процесс позволяет поддерживать содержание железа и ортофосфорной кислоты в растворе на заданных уровнях.
Травление в растворах ортофосфорной кислоты имеет особое значение при подготовке поверхности под окраску. В растворах этой кислоты в ваннах окалина удаляется значительно медленнее, чем в соляной и сернокислотных растворах, удаление ржавчины происходит быстрее. При подаче раствора распылением значительно интенсифицируется процесс, растворы ортофосфорной кислоты можно использовать и для удаления окалины.
При травлении в растворах ортофосфорной кислоты и последующей промывке на стальной поверхности образуется тонкий (1мкм) слой фосфатов железа, который является хорошей основой для последующей окраски. Рекомендуется следующая последовательность операций травления в растворах ортофосфорной кислоты, особенно при их распылении обработка в 10—15%-ном растворе при 75—80° С для удаления окалины и ржавчины, промывка, обработка в 2%-ном растворе с 0,3—0,5% Fe при 60—70° С (для образования слоя фосфатов железа). При регенерации раствора этот процесс становится экономически эффективным, снижается расход кислоты (которая почти в 10 раз дороже соляной и серной кислот), тем самым уравниваются стоимости очистки в этих кислотах. Кроме того, регенерация кислоты обеспечивает постоянство скорости очистки и стабильность качества обрабатываемой поверхности, что является предпосылкой хорошего качества наносимого лакокрасочного покрытия.
Преобразователи ржавчины. Ортофосфорная кислота входит почти во все составы для удаления и преобразования ржавчины. В простейшем случае поверхности со слоем ржавчины небольшой толщины (<50 мкм), предварительно зачищенные щетками, обрабатывают 10%-ным раствором ортофосфорной кислоты, а затем через 24 ч протирают ветошью и окрашивают.
Преобразователи ржавчины содержат, кроме фосфорной кислоты, комплексообразователи, ингибиторы и другие компоненты. Наиболее распространены составы на основе оксикарбоновых кислот (например, таннина), содержащих большое количество гидроксильных и карбоксильных групп, которые, реагируя с окислами железа, образуют таннатные комплексы.
Действие преобразователей ржавчины на поверхности, покрытые окалиной, неэффективно вследствие ее устойчивости к ортофосфорной кислоте. По этой же причине плохо преобразуется ржавчина светло-рыжего цвета, и ржавчина черного цвета, содержащая магнетит.
Преобразователи ржавчины рекомендуется применять в тех случаях, когда нельзя использовать другие методы ее удаления. Их можно применять в сочетании с покрывными лакокрасочными материалами, которые должны обладать высокой адгезией к преобразованному слою ржавчины, связывать остатки кислот или быть стойкими к их воздействию. Окраску производят непосредственно после нанесения и высыхания преобразователей.
Более перспективным способом является грунтование, обеспечивающее одновременно и подготовку прокорродировавших поверхностей под окраску. Грунтовки, используемые для этих целей, содержат некоторые из компонентов, входящих в состав преобразователей ржавчины.
Нейтрализация, промывка и пассивация поверхности. После травления в растворах соляной и серной кислот изделия сложной конфкурации подвергаются ряду операций.
Загрязнение промывных вод остатками кислот, если их количество допустимого (не более 100 мг/л), может привести к снижению адгезии защитных свойств лакокрасочного покрытия, увеличению их склонности к пузыреобразованию и коррозии металла под пленкой.
Окраска изделий должна производиться непосредственно после травления. Срок межоперационного хранения зависит от условий хранения (влажности воздуха в цехе, возможности попадания жидкостей на изделия и т. п.), но не должен превышать 10 ч.
Контроль и корректировка травильных растворов. Концентрацию кислот в травильных растворах определяют прямым титрованием 1 н раствором NaOH. Частота контроля определяется производительностью травильного оборудования (обычно 2—3 раза в смену). Возможен автоматический контроль растворов по электропроводности и плотности.
Содержание железа в травильном растворе определяют колориметрическим методом.
При снижении содержания кислоты раствор корректируют введением концентрированного раствора.
Травильный раствор, содержащий повышенное количество железа, корректируют путем частичной или полной замены раствора.
Фосфатирование
Фосфатирование улучшает защитные свойства и адгезию лакокрасочного покрытия. Фосфатируют главным образом сталь, цинк и оцинкованную сталь.
Фосфатная пленка образуется при окунании изделия в ванну с фосфатирующим раствором или при нанесении раствора распылением в струйной камере, фосфатирование распылением имеет ряд преимуществ перед фосфатированием окунанием: увеличивается равномерность по толщине фосфатного слоя, уменьшается масса и слой получается более плотный. Вследствие пористости фосфатные слои почти не применяют в качестве самостоятельного вида защиты.
Качество и состав фосфатного слоя определяются химическим составом обрабатываемой поверхности, составом фосфатирующего раствора, способом предварительной обработки поверхности, способом подачи раствора и др. Кристаллические цинкфосфатные слои отличаются лучшей коррозионной стойкостью, чем аморфные железофосфатные. Однако последние лучше сопротивляются деформационным воздействиям. В отечественной и зарубежной практике наиболее распространены цинкфосфатные растворы. Основными компонентами их являются: монофосфат цинка, азотная и фосфорная кислоты.
Масса фосфатных слоев должна быть не более 5,0 г/м2, слои должны быть равномерными, плотными, мелкокристаллическими. При большей массе слоев снижается способность покрытия выдерживать деформации; с увеличением степени кристалличности снижается блеск покрытия.
Применяя окислители (нитриты и нитраты), можно снизить температуру растворов и уменьшить длительность фосфатирования с 30—40 до 5—10 мин при фосфатировании окунанием. В случае распыления растворов при отсутствии окислителей фосфатный слой не образуется.
Фосфатные слои хорошего качества образуются в растворах, равновесных при рабочей температуре. Нагрев раствора до этой температуры не должен вызывать выпадение шлама. Применение растворов пониженной концентрации (недонасыщенных) приводит к получению крупнокристаллических фосфатных слоев неравномерной толщины; применение растворов повышенной концентрации (перенасыщенных) связано с непроизводительной затратой реактивов.
Качество фосфатного слоя контролируют визуально, сравнивая с изделием-эталоном. Массу фосфатного слоя можно определить на пластинах-свидетелях, обрабатываемых вместе с изделием по разнице масс образца (с известной площадью) после фосфатирования и после удаления фосфатного слоя. Фосфаты удаляют в течение 10—15 мин в 5%-ном растворе хромовой (или ингибированной соляной) кислоты при 70—75оС. Толщина слоя является менее точной характеристикой фосфатного слоя. Считают, что толщине фосфатного слоя в 1 мкм соответствует масса 1,0—1,5 г на 1 м2 поверхности.
Защитные свойства слоя определяют с помощью 5%-ного раствора NaCl с добавкой 2 г/л K3Fe(CN)6 После выдержки в растворе в течение 30 с образец или изделие промывают холодной проточной водой и обдувают сжатым воздухом. Поры и несплошности фосфатного слоя окрашиваются в синий цвет вследствие образования берлинской лазури.
Пористость фосфатного слоя выявляют и другим методом. В 1 н раствор Na2SO4 на 24 ч погружают фосфатированный образец, после чего в растворе колориметрически определяют количество железа, которое перешло в него сквозь поры фосфатного слоя.
Теплостойкость фосфатного слоя устанавливают по потере массы и выражают в процентах. Фосфатный слой считается теплостойким, если он теряет около 10% первоначальной массы, что для цинкфосфатных покрытий соответствует потере 1 моля кристаллизационной воды на 1 моль фосфата цинка и заметно не влияет на защитные свойства фосфатных слоев.
Кристаллическую структуру фосфатного слоя оценивают визуально либо с помощью микроскопа при увеличениях от 100 до 250. Фосфатные слои хорошего качества должны быть плотными и слабо прочерчиваться ногтем. На них должно быть минимальное количество шлама, который, оставаясь на поверхности, может способствовать вспучиванию лакокрасочного покрытия вследствие осмоса влаги сквозь покрытие.
На качество фосфатного слоя оказывает большое влияние состав раствора и технологические параметры процесса обезжиривания. Не рекомендуется применять сильнощелочные растворы, содержащие силикаты.
Засорение форсунок в струйных камерах — одна из распространенных причин резкого ухудшения качества фосфатного слоя. Необходимо тщательно очищать агрегат не реже 1 раза в неделю с промывкой распылительных контуров и нагревателей ингибированным 5%-ным раствором серной кислоты.
При наличии фильтровальной установки фосфатирующий раствор можно использовать без замены в течение многих месяцев. Во время очистки агрегатов раствор сливают в запасную емкость.
Для приготовления фосфатирующего раствора используют воду с жесткостью не более 4°, так как при наличии солей жесткости усиливается шлакообразование и ухудшается равномерность толщины фосфатного слоя. В районах с повышенной жесткостью воды приготовление фосфатирующего раствора следует производить с частичной подачей деминерализованной воды, чтобы в смеси с технической она обеспечивала жесткость в нужных пределах.
Промывка. После фосфатирования следует промывка изделий водой при комнатной температуре (15—18° С); жесткость воды не должна превышать 4°.
Пассивация. Около 0,2% фосфатированной поверхности приходится на долю пор, в которых металл находится в активном состоянии. После промывки производят пассивацию раствором, содержащим 0,2— 0,25 г/л хромового ангидрида (CrО3),при 45—50° С, в течение 0,5—1 мин. Поскольку в пассивирующем растворе должны быть только ионы шестивалентного хрома Сг6+, его готовят с применением деминерализованной воды. Смену пассивирующего раствора производят 1—2 раза в неделю вследствие того, что в нем накапливаются фосфаты. Перед сливом пассивирующий раствор подкисляют серной кислотой до pH 1,5 и добавляют любой восстановитель, например бисульфит натрия NaHSO3, для восстановления шестивалентного хрома до трёхвалентного. Восстановленный трехвалентный хром осаждают раствором извести.
Сушку фосфатированных поверхностей проводят в течение 2— 5 мин при 110—115° С нагретым воздухом в специальных сушильных камерах. Время сушки изделий сложной конфигурации сокращается за счет предварительной обдувки нагретым воздухом. При сушке легких тонких деталей скорость воздуха на выходе из сопла составляет 2—6 м/с; при сушке тяжелых деталей она может достигать 20—60 м/с. Одновременно с сушкой с поверхности сдуваются отдельные капли и уменьшается количество солей, остающихся после промывки.
При окраске изделий сложной конфигурации, когда качественная отмывка пассивирующего раствора затруднительна, рекомендуется исключать операцию пассивации из технологического процесса, заменяя ее промывкой.
Фосфатирование стали перед порошковой окраской рекомендуется для изделий, эксплуатируемых в жестких условиях атмосферного воздействия. Изделия, эксплуатируемые в закрытых помещениях, могут быть окрашены без предварительного фосфатирования.
Подготовка поверхности алюминия и его сплавов
Для повышении адгезии и долговечности лакокрасочного покрытия поверхность алюминия и его сплавов подвергают специальной химической обработке — хроматированию, фосфатированию или элекохимическому (анодному) октидированию. На поверхности образуются соответственно хроматные, фосфатные или пористые оксидные слои улучшающие адгезию лакокрасочных покрытий.
Хроматирование алюминия и его сплавов производят в растворах хромового ангидрида с добавками фторидов, которые играют роль активаторов пассивной поверхности этих металлов. Время обработки определяется опытным путем для каждого сплава.
Технологический процесс желтого хроматирования состоит из следующих операций:
- Обезжиривания окунанием или распылением в щелочном растворе в течение 2—5 мин при 50— 60° С.
- Промывки в проточной воде в течение 0,5—1 мин при 50° С.
- Хроматирования распылением при 30—50° Св течение 20 с — 2 мин или окунанием при 18—26° С в течение 1—5 мин.
- Промывки в холодной проточной воде в течение 1 мин.
- Сушки теплым и сжатым воздухом (50—60о С), очищенным от масла и пыли.
- Выдержки деталей в течение 24 ч с целью удаления влаги из хроматной пленки.
В тех случаях, когда однократное обезжиривание не обесиечивает достаточную смачиваемость поверхности, его повторяют.
Качество хроматной пленки контролируют визуально. Пленка должна иметь однородный внешний вид, быть электропроводной, обеспечивать хорошую адгезию лакокрасочных покрытий, обладать прочной адгезией с основным металлом. Последнее свойство проверяют протиркой салфеткой, на которой не должно оставаться следов хроматной пленки.
Ввиду наличия, фтористых солей в хроматирующем растворе необходимо строго соблюдать правила техники безопасности: ванны хроматирования оснащать вытяжной вентиляцией, работать только в перчатках, фтористые соли взвешивать в респираторе.
В некоторых случаях перед хроматированием окунанием для получения равномерной хроматной пленки необходимо осветление алюминия и его сплавов после обезжиривания. При этом рекомендуется следующая последовательность операций:
- обезжиривание в щелочном растворе (одно- или двукратное);
- промывка в теплой воде;
- промывка в холодной воде;
- осветление;
- промывка в холодной воде;
- промывка в теплой воде;
- хроматирование;
- промывка в холодной воде;
- сушка при 40—50° С в течение 2 ч;
- выдержка на воздухе в течение 24 ч.
Хроматирование можно производить не только при наличии стационарных установок (ванн, агрегатов обработки распылением), но и методом подачи раствора из шланга сжатым воздухом, нанесения раствора кистью. Эти методы применяют для обработки отдельных крупногабаритных изделий или при ремонтных работах. Струя раствора, подаваемого из шланга, должна быть сплошной без разрывов со скоростью истечения не менее 2 л/мин. Детали обрабатывают пятикратным обливанием всей поверхности с трехминутной выдержкой между обливами. При нанесении хроматирующих растворов смачивают поверхности кистью 5 раз с трехминутной выдержкой после каждого нанесения.

Хроматные слои, образующиеся при хроматировании алюминия и его сплавов, имеют массу от 0,2 до 2 г на 1 м2 обрабатываемой поверхности, они нерастворимы в воде и органических растворителях, растворимы в концентрированных кислотах и щелочах. Слои обладают незначительным электросопротивлением и не препятствуют электросварке. Детали, сваренные электродуговым методом, хроматируют после сварки. Детали, подвергаемые точечной сварке, — до сварки.
Несмотря на небольшую толщину (от 0,1 до 1 мкм), хроматные слои можно использовать для межоперационной защиты алюминия и его сплавов включая сплавы с высоким содержанием магния. Они термофильны до температуры плавления алюминия (670° С), хорошо деформируются и не отслаиваются при любой деформации.
Оборудование для химической подготовки поверхности изделий под окраску
Оборудование для подготовки поверхности методом окунания. В условиях мелкосерийного и единичного производств химическую подготовку поверхности изделий проводят последовательно, погружая их в ванны с раствором электролита или водой. Размеры ванн определяются размерами изделий, программой предприятия, технологическим процессом подготовки поверхности.
Для ванн обезжиривания изделий щелочными растворами каркас изготовляют из профильного проката, а стенки из листовой стали.
Нагрев раствора до необходимой температуры и поддержание ее в процессе работы осуществляются с помощью змеевиков. В качестве теплоносителя обычно используют насыщенный пар. В верхней части ванны имеется сливной штуцер с карманом для удаления накапливающихся жировых загрязнений, а в нижней части — штуцер для полного слива раствора и промывки ванны. Стенки ванн, как правило, изготовляют двойными, пространство между ними заполняют шлаковой, минеральной ватой или другим теплоизоляционным материалом. Для удаления испарений имеется вытяжная вентиляция (зонты, бортовые отсосы).
Ванны для травления, нейтрализации, пассивирования и промывки по конструкции сходны с ваннами для обезжиривания.
Внутреннюю поверхность ванн для растворов кислот с температурой до 60° С футеруют внутри кислотоупорными материалами (резиной, диабазовыми плитками на кислотоупорном цементе, фаолитом, винипластом). Ванны для растворов кислот с температурой выше 60° С изготовляют из нержавеющей стали.
Растворы в ваннах травления нагревают острым паром или паровыми змеевиками из кислотостойких сталей, свинца или графитопласта. Первый способ нежелателен, так как приводит к снижению концентрации травильного раствора и соответственно скорости очистки.
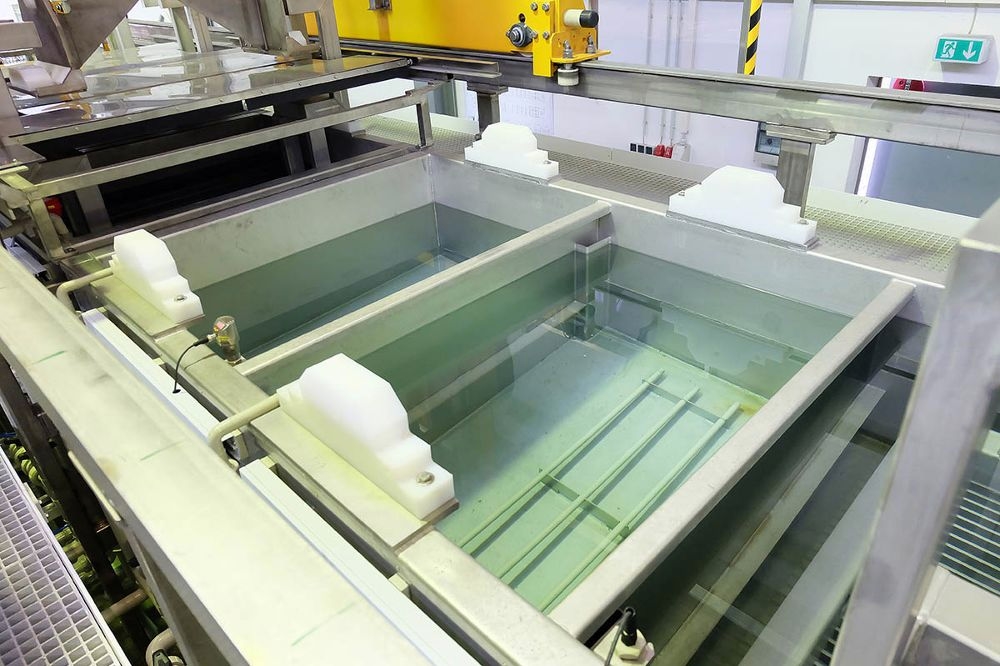
Ванны для фосфатирования представляют собой сварные емкости из нержавеющей стали Х18Н9Т, которые могут быть легка очищены от шлама, так как дно выполнено либо в виде двух конусов, либо с уклоном к одной из боковых сторон. Шлам, который засасывается со дна специальным насосом, может подаваться в отдельный сборник. Раствор нагревают погружными элементами, причем нагреватель и люк для удаления шлама располагают у противоположных сторон ванны. Ванна должна быть снабжена автоматическим терморегулятором и может обслуживаться вручную либо автоматическими транспортными средствами.
При обработке мелких деталей или изделий ванна фосфатирования может быть частью установки карусельного типа.
Для проведения нескольких операций химической подготовки поверхности необходимо иметь ряд ванн. В таких случаях их объединяют в одну установку с механизированной загрузкой и переносом изделий из ванны в ванну.
Механические методы
К механическим методам относятся очистки: гидравлическая, электрогидравлическая, гидроабразивная, дробеструйная, дробеметная, пароструйная, ручным и механизированным инструментом, на станках и в галтовочных барабанах, в том числе вибрационных.
К преимуществам этих методов относятся:
- 1) возможность обработки всех видов изделий чугунных, стальных, из легких и цветных металлов, в том числе крупногабаритных (любой длины и высоты), мелких деталей с сохранением их формы и размеров; некоторые механические методы могут применяться при очистке изделий из древесины, тканей, кожи, пластмасс, резины, стекла и других неметаллических материалов;
- 2) создание оптимальной шероховатости поверхности, обеспечивающей высокую адгезию лакокрасочного покрытия к окрашиваемой поверхности;
- 3) возможность обработки изделий и деталей непосредственно на рабочих местах без капитальных сооружений (механизированным инструментом, беспыльными дробеструйными установками);
- 4) возможность включения процессов дробеструйной, дробеметной, гидравлической очистки в поточные и конвейерные линии;
- 5) отсутствие солей на очищенной поверхности и необходимости их удаления промывкой;
- 6) исключение из технологического процесса операции сушки (за исключением гидроабразивного и гидравлического метода очистки).
К недостаткам механических методов очистки относятся: значительная стоимость обработки, особенно при ручной очистке; малая производительность (за исключением дробеметной и гидравлической очистки); наклеп обрабатываемой поверхности при дробеметной очистке.
Очистка ручным и механизированным инструментом
Преимуществом этого метода является возможность путем замены одной рабочей части другой выполнять разнообразные операции: шлифование плоскостей, удаление окалины, ржавчины, старого лакокрасочного покрытия, снятие заусенцев и скругление острых кромок, зачистку сварных швов, очистку поверхностей поковок и отливок от формовочной земли, удаление с поверхности проката пузырей, свищей, рябизны, шероховатости и т. п. Таким инструментом легко обрабатывают поверхности легких и цветных металлов, древесины, пластмасс, кожи, стекла и других материалов, применяемых в машиностроении и подвергающихся окраске.
На крупногабаритных изделиях обработку ручным и механизированным инструментом можно производить одновременно с другими работами, не снимая отдельные детали для обработки на станках.
Производительность труда при очистке механизированным инструментом повышается в 5, а во многих случаях более, 15 раз по сравнению с ручной очисткой.
Недостатком ручного и механизированного инструмента является быстрый износ и необходимость частой замены рабочих частей. В качестве рабочей части ручного и механизированного инструмента для подготовки поверхности под окраску применяют щетки разных типов, абразивные круги, шлифовальные шкурки и ленты, зубила и ударники в рубильных молотках.
Щетки характеризуются типом, материалом и диаметром ворса, свободной длиной ворса, плотностью (густотой) рабочей части, шириной и диаметром щетки и материалом ступицы. Основные типы щеток: дисковые, цилиндрические (роликовые), торцовые (чашечные) и концевые. Материал ворса —стальная проволока разных марок, латунная проволока, щетина натуральная и синтетическая, волос, корд, растительные волокна.
Абразивные инструменты состоят из зерен абразивного материала, сцементированных связкой. Для упрочнения кругов применяют: графитовый наполнитель; армировку проволочной сеткой, стекловолокном и тканевыми прокладками, что позволяет увеличить окружную скорость резания до 50 (вместо 35) м/с, а иногда до 100 м/с.
Шлифовальные шкурки и ленты изготовляют на бумажной или тканевой основе, а диски — на фибре. К основе приклеивают абразивный порошок разной зернистости. Существуют шкурки с основой в виде сетки, на обе стороны которой нанесен абразив, а также гибкие ленты, в которых запрессован абразив. Шлифовальные листы и шкурки применяют на больших поверхностях при слабых усилиях резания.
Рабочая поверхность шлифовальных лент в несколько раз больше, чему абразивных кругов. Ленты обеспечивают лучшее рассеивание тепла и механизацию обработки даже сложных фасонных поверхностей; они работают эластично, плавно, без ударов и не требуют балансировки. В отличие от абразивных кругов при износе ленты не меняется скорость резания.
Абразивное зерно наносят на шкурки и ленты электростатическим (ЭС) или механическим (МС) методом. Производительность ленты с электростатически нанесенным абразивом на 30—50% больше, чем ленты с механически нанесенным абразивом.
Абразив приклеивается к неводостойкой шкурке мездровым клеем вязкостью 5—6° по Энглеру, а к водостойкой — клеем ФМ-4 или ФМ-3.
Механизированный инструмент подразделяется на пневматический и электрический. Пневматические инструменты просты в эксплуатации, имеют малый вес по отношению к развиваемой мощности, безопасны в работе, позволяют свободно регулировать крутящий момент и скорость вращения шпинделя и могут быть заторможены (до полной остановки) без вреда для дальнейшей работы, не боятся перегрузок и легко приспосабливаются к разным условиям работы (во влажной среде, при высоких температурах и большой запыленности воздуха). Поэтому, несмотря на более низкий к. п. д. (7—11% вместо 35— 70% для электрического инструмента), они широко применяются, но для них нужны мощные компрессорные установки и дополнительный обслуживающий персонал. Они менее экономичны, чем электрические, и сильно снижают полезную мощность при понижении давления сжатого воздуха. Так, при давлении воздуха 5 кгс/см2 машинка вращается с частотой 280 об/мин, имея полезную мощность 2,5 кВт, а при уменьшении давления до 3 кгс/см2 частота вращения снижаегся до 210 об/мин, а полезная мощность—до 1 кВт; пневматический очистной молоток соответственно снижает число ударов с 900 в минуту с силой 4 кгс до 720 ударов в минуту с силой 3,2 кгс.
При работе с электрическими машинками высокого напряжения требуется соблюдать особую осторожность во избежание поражения током. По этой причине их часто используют с понижающими трансформаторами (со снижением напряжения до 36—12 В).
Основными техническими характеристиками пневматического инструмента являются количество потребляемого воздуха и число оборотов в минуту или для инструмента ударного действия число ударов в минуту; для электрического инструмента — мощность и число оборотов в минуту.
По конструкции рабочей части машинки бывают прямые, торцовые и угловые. В качестве привода используют: в пневматических машинках — ротационные, лопастные или турбинные двигатели; в электрических — электродвигатели переменного или постоянного тока или универсальные, в некоторых случаях с гибким валом. Повышенной производительностью обладает электромеханическая щетка, имеющая пневматический ротационный двигатель.
Инструмент и его рабочую часть выбирают в зависимости от условий обработки изделий.
Для очистки больших поверхностей от ржавчины и непрочно сцепленной окалины можно применять пневматические угловые щетки — реверсивные с двумя вращающимися в разные стороны щетками — или электроинструмент с шарошками. Наиболее удобными являются угловые головки, так как они могут быть использованы при работе в любом положении и на различных поверхностях. Прямые головки неудобны для очистки в углах и на поверхностях, имеющих выступы.
Пневматические молотки обеспечивают удаление толстой и прочной окалины, прочных пластов ржавчины, неровностей сварных швов, заусенцев и других дефектов металлической поверхности. Кроме пневматических молотков основных типов с короткими ручками и одним ударником, применяют молотки с удлиненной рукояткой и пучковые с многочисленными бойками-ударниками. Большие плоскости листового проката очищают передвижными (напольными) щетками с цепной и ременной передачей.
Для очистки внутренних поверхностей труб диаметром от 30 мм до 2 м применяют специальные машинки с радиально расположенным ворсом щеток.
Гидроабразивная очистка.
В качестве абразива применяют кварцевый песок, молотый гранит, абразивные зерна, молотый шлак и т. п.
Гидроабразивные установки различаются системами смешения суспензии, подачи ее к струйному аппарату (соплу) и ускорения ее движения.
В некоторых установках абразив, смешанный с водой в баке, поддерживается во взвешенном состоянии пропеллерной мешалкой, вращающейся от электродвигателя, и в виде суспензии по трубопроводу подается в пистолет, из которого сжатым воздухом, поступающим по воздухопроводу, направляется на обрабатываемую поверхность детали. После этого суспензия стекает в нижнюю часть камеры и самотеком возвращается в бак. Эта установка применяется при небольших объемах работ и сравнительно низкой производительности.
Существуют установки без мешалки и насоса, в которых суспензия перемешивается воздухом, подаваемым по трубе (в дне бака) в коллектор с отверстиями, и эжектируется пистолетом. Эти установки просты в эксплуатации и экономичны, но малопроизводительны.
Широкое распространение получили установки с нагнетанием суспензии насосом, и последующим ускорением ее движения воздухом или лопастями ротора. В некоторых установках суспензия поступает самотеком без эжекции струи, но с ускорением воздухом. Существуют установки, в которых абразив и вода подаются раздельно, а ускорение струи осуществляется давлением воздуха.
Основным преимуществом гидроабразивной обработки перед другими методами является почти полное отсутствие пылевыделения. Производительность установок в 2—3 раза выше, чем механизированных инструментов, но на 10% ниже пескоструйных установок. Недостатками этого метода является быстрая коррозия очищенных влажных поверхностей и необходимость в связи с этим добавления в суспензию пассивирующих веществ и последующей обработки поверхности пассиваторами, загрязнение смежных поверхностей, дополнительный расход рабочей силы, материалов и времени на промывку и сушку, вредное физиологическое действие некоторых пассиваторов.
Пассивирующие вещества: 0,5% бихромата калия, 0,5—2% тринатрийфосфата или 0,5—1% нитрита натрия от веса пульпы.
Промывку очищенных поверхностей от остатков пульпы и грязи проводят холодной и затем горячей (90—95 С) водой с добавкой 0,2% бихромата калия или 5—10% нитрита натрия. Рекомендуемая для гидропескоструйных аппаратов грануляция зерен песка 0,5—0,8 мм.
Для гидроабразивной очистки изделий из разных металлов применяют смеси воды и кварцевого песка.
Все более широко применяют метод гидроочистки и гидропескоочистки с помощью гидромониторов и насосов высокого давления.
Дробеструйная и пескоструйная очистка.
Для дробеструйной и дробеметной обработки применяют чугунную или стальную дробь либо металлический (стальной) песок определенной зернистости.
Стальную дробь и металлический песок подбирают так, чтобы они были из того же материала, что и очищаемые детали, или более твердые. Для очистки деталей из нержавеющей стали применяют дробь из стали X18Н9; для алюминиевых деталей — алюминиевую дробь; для латунных и медных изделий — дробь латунную или медную; для очистки латунных деталей измерительных приборов, часов, счетноаналитических и пишущих машин — бронзовый скрап; для очистки тонкостенных алюминиевых, магниевых и других деталей, когда требуется сохранить размеры и прочность деталей, применяют дробленую скорлупу грецких орехов или дробленые фруктовые косточки. Сухой кварцевый песок можно использовать для очистки пескоструйным аппаратом только на открытом воздухе при обработке крупногабаритных изделий (бензохранилищ, мостов, судов и т. п.). В закрытых помещениях очистка кварцевым песком запрещается.
Очистка дробью и металлическим песком имеет следующие преимущества перед очисткой кварцевым песком: расход стальной дроби и металлического песка незначительный, они могут быть использованы многократно и длительное время без замены; процесс подготовки дроби прост; расход воздуха небольшой; срок службы сопел больше, чем при пескоструйной очистке; условия труда лучше, так как нет кварцевой пыли; имеется возможность полной механизации и автоматизации процесса очитки.
Особенностью аппаратов для беспыльной очистки поверхности металла является наличие устройства для отсасывания абразивной пыли из зоны очистки. Такие аппараты выпускают передвижными или переносными.
Очистка на станках
Изделия несложной формы (трубы, листы) рекомендуется очищать на специальных станках которые при незначительных эксплуатационных расходах обеспечивают высокую производительность. В качестве рабочего органа станки имеют цилиндрические щетки большой ширины, шлифовальные, шкурки, шлифовальные ленты и другие абразивные материалы.
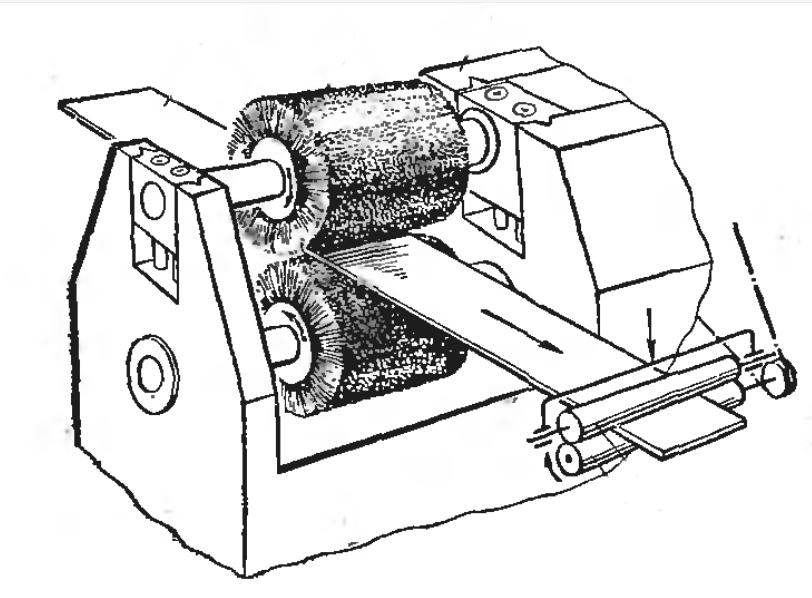
На многих машиностроительных заводах применяют подвесные станки с абразивными кругами для зачистки поверхности крупных изделий, так как их перемещения затруднены вследствие большого веса.
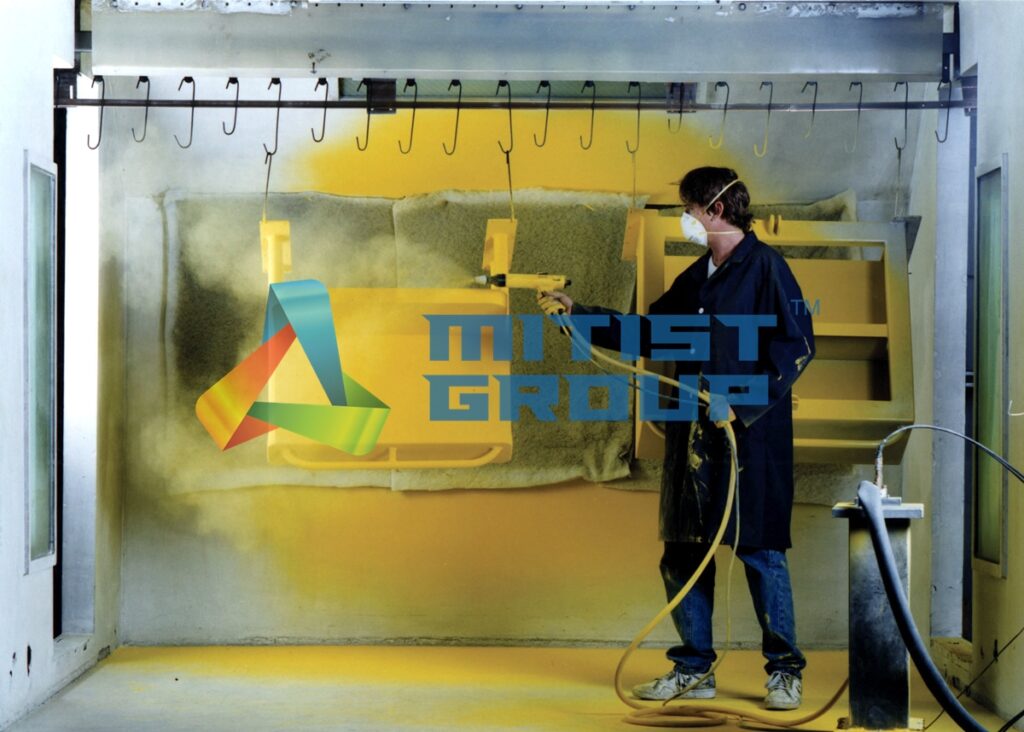
Порошковая покраска в «МИТИСТ ГРУПП»
Оказываем услуги порошковой покраски металлических изделий с 2012 года. Мы предлагаем обширный выбор цветов RAL, выполняем предварительную обработку поверхностей особыми составами. Выполняем срочные заказы небольших объёмов. Общий габарит камеры полимеризации — 3000*2000*1500. Минимальная сумма заказа, при окраске в один цвет — 5 000₽